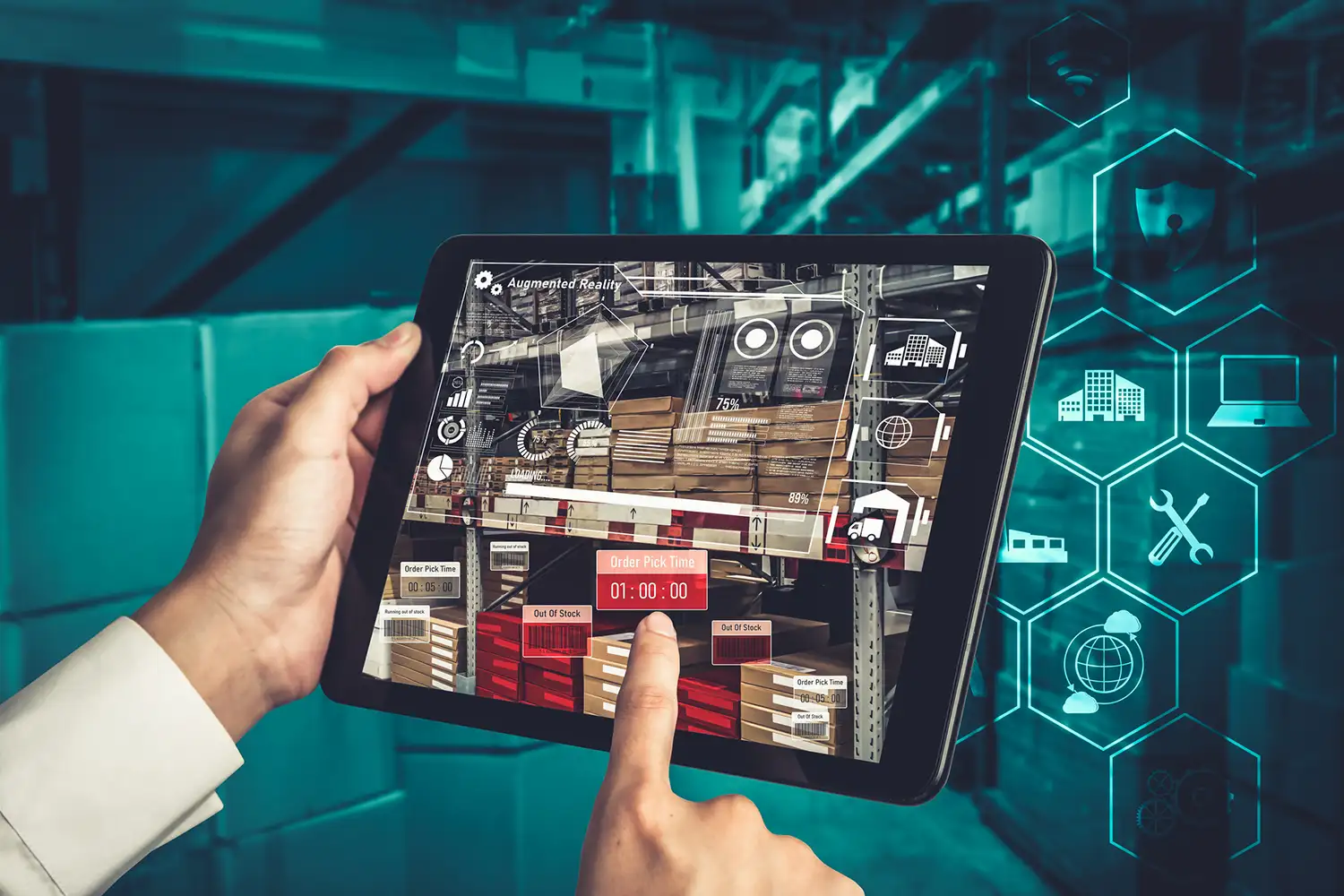
Any thriving business hits a point of success that requires the next step to be taken to continue the upward trajectory. If you have been hardworking and determined enough to begin seeing the fruits of your labor develop into true business success; Congratulations! It may now be time for you to create and implement an inventory system for your business so that it can continue to grow and profit. If you’re thinking now is the time to elevate your inventory system/process at work, read on for steps you must take to reach this next level of business achievement.
Define Your Needs
The first step of creating a successful inventory system is defining what exactly it is you need to keep track of to improve your business. Take note of all items you decide you need to keep track of. You also want to note how many of each item you currently have, and any pertinent specifics about each item that will be inventoried (color, expiration dates, etc.) These notes will be the starting point for all future inventories.
Designate An Area
Next you need to find and designate a space to become your stockroom. If you don’t have a full room to dedicate to your inventory, designate a smaller space or closet within the office or building. If you have an excessive number of items or very large/heavy products, you might find an off-site storage space, or secondary building, depending on your situation and business model. If you don’t need direct access to all items all the time (old files, business products, etc.) consider having samples of stored items available so that you can refer to them if you need examples. This way items are accessible, even if you don’t always have the full stock of supplies on hand.
Establish Categories
Once you’ve identified items to be inventoried and have designated a storage space to stock these items, you need to establish categories. Creating categories for your stock will make it easier to consistently find and manage items. You may consider color-coding each of the categories to make the system even clearer to outsiders, new employees, stock delivery drivers, etc.
Ordering Schedule
A pre-determined ordering schedule that makes sense for the business’s needs is essential. Determine the importance of each item you’ll be inventorying and how often you use each so that you can determine how often you need to place restock orders. You want this ordering schedule to keep up with the inventory and ensure items (such as medical supplies or paper products) are in stock when needed. Have an ordering checklist available/accessible and designate one person to this task to minimize over-ordering. Designate one or two days per week to ordering product. When deciding whether one or two ordering days is necessary you should consider:
- the length of time it takes the items to be shipped and received
- the ordering guidelines for the products
- how frequently your company uses these items
- how often your company runs out of the items
Factoring in all the above, make an educated decision about which day(s) ordering will take place, and then stick to your ordering schedule once it has been decided. It’s important you’re also careful not to overstock, thus creating an entirely new issue (clutter).
Implementing a Tagging or Barcode System
Depending on the size of the weekly orders, you may want or need to implement a more advanced system. Implementing a tag or barcode system allows you to track items accurately and efficiently in real-time. A tag or barcode system also helps to reduce errors that may occur and allows for a smoother, faster process. Another benefit of taking your inventory to this next level is that, depending on the system, you can usually control who has access to the inventory.
Set Aside Times to Audit
Once you have your system in place, you’ll regularly want to conduct audits to verify the inventory count is accurate. If you have items that expire, you may want to consider doing this more regularly to make sure those products are getting properly rotated and older product is getting used first (before the expiration). Audits will not only keep your inventory count accurate, but they will help you catch other discrepancies such as items improperly marked, or items placed in the wrong location. Regularly auditing will also help you monitor your system itself. As you find and review discrepancies you can analyze how the inventory system is working for you and adapt or improve it as the business’ needs change. This will show you how much you are spending and if there are any areas you can revise to save money and increase working capital.
Conduct Training
You will need to have a training process in place for any employees who will need or have access to the inventory. Areas with a need for training include:
- Data entry
- Inventory process (scanning barcodes or tags and the digital system)
- Understanding the proper practices for inventory management
Again, you’ll also want to ensure the employee overseeing the ordering checklist is familiar with the inventory program and comfortable using it. Make sure all other employees have a good understanding of the items held in storage so they can keep up with the system in an efficient manner as well.
If you read this and think it sounds like something that will benefit your business but you’re still feeling overwhelmed or simply want help getting started; please let us know! One of our Productivity Consultants would love to help get your inventory system up and running on the path to success. Send us an email at info@sortedout.com or leave a comment below and we’ll be in touch!
Looking forward to hearing from you!
Tonia
Request a Consultation
There are so many ways that organization can help take back a space that is overwhelming and bring it to functional! We are excited to help start your journey to an organized and productive space.